Thermoplastic starch (TPS) has some drawbacks including: Poor heat resistance leads to melting or degradation at high temperatures; Low tensile strength and brittle nature, make it unsuitable for certain applications; Hydrophilic nature, making it susceptible to water absorption and swelling; Sensitivity to pH and other environmental factors leads to changes in properties over time; Higher cost compared to traditional petroleum-based plastics;
Introduction
In general, starch films have high tensile strength, but are brittle and exhibit almost no elongation at break (Briassoulis, 2004). For instance, at 15% water content, extruded starch has poor mechanical properties and is inadequate for film applications (initial tensile strength 20–30 MPa and elongation at break 10–15%) (Imam et al., 1995). Moreover, these properties are affected by relative humidity and, thus, by the corresponding changes in Tg. At low relative humidity, there are problems with brittleness, whereas at high relative humidity, with softness. In addition to moisture sensitivity, TPS materials change their time-dependent mechanical properties (also called “postprocessing aging”). In order to overcome these limitations, different strategies are often adopted, such as: (i) chemically modified starch in formulations; (ii) suitable plasticizers; (iii) association of biodegradable, renewable, or synthetic polymers to thermoplastic starch; and (iv) surface modifications of starch plastics.
TPS from modified starches
Starch-based materials have been developed through chemical modification by well-known organic reactions, to obtain material with improved water sensitivity and mechanical performance (Fringant, Desbrières, and Rinaudo, 1996; Demirgöz et al., 2000; Wilpiszewska and Spychaj, 2007).
Starch esterification by acetylation has been shown to be an efficient chemical modification for obtaining TPS-based materials with reinforced hydrophobicity and higher thermal stability (Fringant, Desbrières, and Rinaudo, 1996); better properties are achieved with degrees of substitution (DS) higher than 1.7. The properties of starches modified by chemical derivatization are also some options for TPS materials; they depend greatly on DS and the length of the introduced alkyl chain; the higher the DS and the longer the aliphatic chain the better are the hydrophobic properties (Wilpiszewska and Spychaj, 2007) and blends with cross-linking modified starch by hydroxyl groups and tri-sodium tri-meta phosphate (Demirgöz et al., 2000).
However, according to Avérous (2004), the strategy of chemical modification is strongly limited by: (i) the toxicity and the diversity of byproducts obtained during the chemical reactions, (ii) the high cost of modification and product purification stages, and (iii) the unfavorable alterations in TPS mechanical properties caused by chemical reactions.
Plasticizers and biodegradable polymers in TPS
Both aging through crystallization and water sensitivity are affected by the choice of plasticizer. Thus, it is very important for the application and development of starch materials to choose a plasticizer that is able to impart flexibility to TPS materials and to suppress retrogradation during the aging time. In order to achieve this objective, several plasticizers have been incorporated with pure thermoplastic starch, such as water, glycol, sorbitol, urea, amide, sugars, and quaternary amine. Recently, it was suggested that the use of high glycerol content or of plasticizers with other polar groups that have stronger interaction with the starch molecular structure than glycerol should be an effective approach to restrain aging (Shi et al., 2007). The addition of glyceryl monostearate (GMS) as surfactant to TPS films decreased their retrogradation tendencies (Mondragón, Arroyo, and Romero-García, 2008) and this effect is attributed to the formation of amylose-GMS complexes which is favored over the amylose retrogradation.
Starch has been also widely blended with biodegradable polymers, including polycaprolactone (Avérous et al., 2000), polylactic acid (Zhang and Sun, 2004), polyhydroxybutyrate (Thiré, Ribeiro, and Andrade, 2006), and poly(hydroxyester ether) (Willet and Doane, 2002). Thermoplastic starch blended with thermoplastic polyesters, such as polycaprolactone (PCL), is the most popular base film (Bastioli, 2000). Commercially, TPS is used alone mainly in soluble compostable foams, such as loose fillers, and other expanded items as a replacement for polystyrene. These films are biodegradable, compostable, and fulfill the requirements of different application fields, such as packaging and agriculture. Thus, the association of TPS with other biodegradable compounds is a promising strategy to obtain compostable multiphase materials with improved properties. The relationships among structure, process, and properties of biodegradable multiphase materials (i.e., blends, composites, and multilayers) based on TPS have been reviewed recently by Avérous (2004).
Biodegradable blends of TPS and waterborne polyurethane (PU) obtained from castor oil presented improved mechanical properties, surface and bulk hydrophobicity, and water resistance, as compared to pure TPS films (Lu et al., 2005). Glycerol-plasticized blended films of wheat TPS and polycaprolactone obtained by extrusion and injection molding (Avérous, et al. 2000) show phase separation with significant improvement of stability and hydrophobicity due to the presence of polycaprolactone.
Effects of multilayer structures on TPS constitution
In addition to blends, the association of starch and other polymers can be obtained by multilayer structures. These structures are composed of an internal layer of TPS and two external layers of hydrophobic polymer. Compared to blends, in general, multilayer structures present higher water resistance, because moisture sensitivity is not fully addressed in a blend as a result of starch phase distribution close to the surface (Avérous, 2004).
Starch-based materials coated with water-resistant biodegradable polyesters are viable for a broader range of uses, including those typical of food preparation, packaging, and consumption (Shogren and Lawton, 1998). This method involves: (i) the application of a natural resin layer, such as shellac or pine rosin, to the surface of a starch-based article and (ii) subsequent application of a continuous layer of a water-resistant polyester, such as poly(beta-hydroxybutyrate-co-valerate) (PHBV) and poly(lactic acid) (PLA).
For plasticized starch–polyethylene multilayer systems, the compatibility of starch and polyethylene is achieved through maleic anhydride functionalized polyethylene (PEg) (Dole et al., 2005). The use of the starch–multilayer structure (PE/PEg/starch/PEg/PE) improves gas barrier properties at high relative humidity as compared to existing commercial multilayer systems (PE/PEg/EVOH/PEg/PE). The higher quantity of water sorbed by TPS and the specific water sorption isotherm of starch significantly extended the water equilibration time in the hydrophilic inner layer (Dole et al., 2005).
Manufacturing starch composites with reinforced natural fibers is another way to achieve TPS-based multilayer materials with improved properties (Dufresne and Vignon, 1998; Curvelo, de Carvalho, and Agnelli, 2001; Avérous and Boquillon, 2004). Improvements of TPS-reinforced film performance can be attributed to usual matrix reinforcement and to the interrelations of the fiber matrix (Avérous, 2004). According to Dufresne and Vignon (1998), the water resistance of starch-based plastics can be improved by adding a small amount of commercial cellulose fibers up to 15% w/w. Extruded and injection-molded TPS sheets reinforced by cellulose and lignocellulose fillers exhibit improved thermal resistance compared to nonreinforced sheets (Avérous and Boquillon, 2004). Mechanical behavior of these reinforced biocomposites changes according to the filler content, fiber nature, and fiber length. Composites prepared with regular corn starch plasticized with glycerol and reinforced with short cellulosic fibers (16% w/w) from bleached pulp (Curvelo, de Carvalho, and Agnelli, 2001), increased 100% in tensile strength and more than 50% in modulus in relation to nonreinforced films.
Recently, nanoscale fillers have been incorporated into starch blends to enhance thermal, mechanical, and processing properties of the products. Two kinds of nanoparticles have been tested in TPS composites: whiskers obtained from cellulose (Samir, Alloin, and Dufresne, 2005; Angellier et al., 2006) and organoclays (McGlashan and Halley, 2003; Huang, Yu, and Ma, 2004).
Surface modification
Surface modification is a suitable approach to alter superficial physical and chemical properties of starch films, such as hydrophilicity and water uptake, without affecting their bulk properties. It can be accomplished, for instance, by chemical reactions between an external reagent and superficial hydroxylic groups of starch or by depositing a protective layer over the starch film or sheet surface (coating process). The surface of compress-molded corn starch films is modified by reaction with coupling agents (isocyanate, phenol, blocked isocyanate, epoxy and acid chloride moieties, i.e., small molecules and polymeric ones) (Carvalho, Curvelo, and Gandini, 2005) and the polymeric reagents coupled simultaneously with OH groups, immobilizing the latter species. Dipping followed by heating proved to be an adequate process for surface modification, which led to a decrease of the hydrophilic character of TPS films. Decreasing water uptake and improving mechanical properties of glycerol–cassava starch films are achieved by coating a chitosan solution on starch film (Bangyekan, Aht-Ong, and Srikulkit, 2006). An increase in chitosan coating concentration results in a significant increase in tensile stress at maximum load and tensile modulus and a decrease in elongation at break. The combination of (i) hydrogen bonding, (ii) opposite charge attraction between chitosan cations and negatively charged starch film surface, (iii) hydrophilicity, and (iv) compatible water activities provides a good adherence between the two layers.
Another approach to overcome starch limitation is the protection of starch materials from humidity changes with a thin polymeric layer, deposited by plasma polymerization (or glow discharge polymerization). Plasma technology has become an important industrial process, used to alter chemical and physical properties of polymeric surfaces without affecting their bulk properties. Glow discharge polymerization is a specific type of plasma chemistry, which consists of complex reactions between charged and neutral plasma species, between plasma and surface species, and between surface species (Chan, Ko, and Hiraoka, 1996; Yasuda, 1981). Unlike conventional polymers, plasma polymers do not consist of chains with a regular repeating unit, but tend to form cross-linked networks. Deposition of thin films by plasma polymerization offers several advantages over conventional coating techniques: (i) the process may occur in a single reaction step, (ii) a nanometer-thick coating is obtained, (iii) good adhesion between film and substrate is generally achieved, (iv) the deposition of the film is fairly uniform over the entire surface, and (v) problems with residual solvents are avoided (Chan, Ko, and Hiraoka, 1996). The process involved in macromolecular surface modification in cold plasma environments was recently reviewed by Denes and Manolache (2004).
Ultra-thin, glass-like SiOx coating (20–50 nm thick coating) plasmadeposited on different starch-based films is proposed as a technical solution to improve their barrier properties against water vapor and gases (Johansson, 2000). Starch foils coated in a radiofrequency glow discharge with two different monomers, hexamethyldisilazane (HMDSN) and hexamethyldisiloxane (HMDSO). Argon feeds at radiofrequency discharge powers of 5 and 2 W improved their water-repellent properties without affecting the biodegradability of foils (Behnisch et al., 1998).
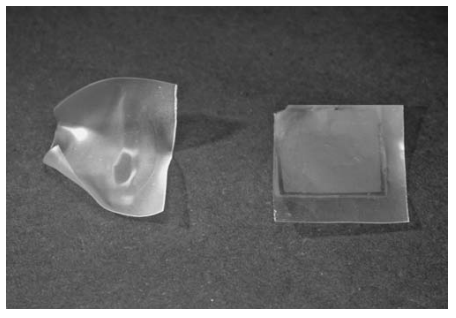
Similar results are obtained with cast corn starch films coated by low-pressure plasma polymerization in a 1-butene atmosphere (Andrade, Simão, and Thiré, 2005). For partially gelatinized coated films, an average reduction of 52% in water absorption is observed, independent of coating thickness and for completely gelatinized coated films, a maximum reduction of 90% in water absorption is observed for coatings 80 nm in thickness. When 1,3-butadiene is used as monomer to plasma polymerization, the water absorption of partially gelatinized coated films is reduced up to 80% (Simão et al., 2006a). Unmodified and 1-butene plasma-modified corn starch films can be seen in Figure 1. The unmodified film folded due to water absorption, whereas the plasma-modified film remained visually intact, illustrating the protection against water imparted by plasma coating.
The process based on plasma polymerization in a methane atmosphere followed by sulfur hexafluoride (SF6) plasma treatment can also improve water repellence of corn starch films (Simão et al., 2006b). The increase of surface hydrophobicity may be related to the resulting topography originated from SF6 etching of the homogeneous coating obtained by previous methane plasma treatment.